Was ist OEE, wo kommt der Begriff her und was ist an OEE anders?
Overall Equipment Effectiveness (zu Deutsch auch Gesamtanlageneffektivität) verbirgt sich hinter dem Kürzel OEE. Die OEE ist ein Messinstrument, mit dem Verluste eine Maschine aufgedeckt und dann mithilfe von Optimierungsansätzen zielgerichtet bekämpft werden. Schöpfer dieser Produktivitätskennzahl ist der Japaner Seiichi Nakajima und das Japan Institute for Plant Maintenance im Zusammenhang mit dem Verbesserungsansatz Total Productive Maintenance. Die Weiterentwicklung dieses Ansatzes wurde inzwischen zum umfassenden Managementsystem Total Productive Management (TPM) realisiert. Auch wenn die Gesamtanlageneffektivität anfangs nur im Bereich TPM angewandt wurde, ist es zwischenzeitlich ein unverzichtbares Instrument für andere betriebliche Verbesserungsprogramme, wie beispielsweise Lean Production und Six Sigma. Die OEE misst die gesamte Bandbreite der Effektivitätsverluste von Produktionsanlagen und verdeutlicht, welche maschinen- und prozessabhängigen Verluste minimiert werden müssen.
Die Gesamtanlageneffektivität fasst die Parameter Zeit, Stückzahl und Qualität zusammen und macht sie für das Produktionsteam nachvollziehbar. Darüber hinaus kann das Produktionsteam die Gesamtanlageneffektivität steuern, denn alle Parameter sind direkt oder indirekt durch das Team beeinflussbar. Damit ist – im Gegensatz zu vielen anderen Kennzahlen im Produktionsbereich – die Gesamtanlageneffektivität ein Instrument, das sich das Produktionsteam völlig zu eigen machen kann und dass damit beste Voraussetzung für effektives Shopfloor-Management bietet.
Maschinenverluste als Ansatzpunkte für die OEE berechnen
Die ideale, vollkommen wirksame Maschine sollte ohne Unterbrechung mit Höchstgeschwindigkeit laufen können, ohne auch nur ein fehlerhaftes Erzeugnis zu produzieren. Da diese Idealvorstellung in der Wirklichkeit unerreichbar ist, werden drei wesentliche Verlustbereiche gegeneinander abgegrenzt:
- Verfügbarkeit,
- Leistung und
- Qualität.
Diese Verlustbereiche werden weiter aufgeschlüsselt in die sechs großen Verlustarten:
- Störungen (Verfügbarkeitsverluste),
- Wartezeiten (Verfügbarkeitsverluste),
- Kurzstillstände (Leistungsverlust),
- Reduzierte Geschwindigkeit (Leistungsverlust),
- Ausschuss (Qualitätsverlust),
- Nacharbeit (Qualitätsverlust).
OEE berechnen
Sie sehen gerade einen Platzhalterinhalt von YouTube. Um auf den eigentlichen Inhalt zuzugreifen, klicken Sie auf die Schaltfläche unten. Bitte beachten Sie, dass dabei Daten an Drittanbieter weitergegeben werden.
Die Grundlage für die OEE berechnen ist so einfach wie brillant: Grundlage ist stets die theoretische möchstmögliche Ausbringung einerseits, und die wirkliche Ausbringung fehlerfreier Produkte andererseits. Der erste Aspekt bezieht sich auf das Ziel, der zweite Aspekt auf die aktuelle Lage. Damit skizziert die OEE nicht nur die „Verlustlandschaft“ zwischen diesen beiden Aspekten, sondern ist auch – und das ist wichtiger – für den Personenkreis transparent, der jeden Tag damit arbeiten muss, also für Maschinenbediener, Techniker, Ingenieure usw.
Grundlage für die OEE berechnen ist die mögliche Produktionszeit (= verfügbare Zeit – ungeplante Zeit) d. h. Stillstandszeiten, beispielsweise wegen Mangel an Aufträgen, gehen nicht in die Gesamtanlageneffektivität ein, weil dann kein Bedarf besteht und die Herstellung auf Lager für sich wiederum einen Verlust ergäbe! Wird die mögliche Produktionszeit als Grundlage genommen, wirft die OEE-Bestimmung drei Fragen auf:
1. Läuft die Maschine, oder läuft sie nicht?
Wenn die Maschine läuft (wenn sie Waren produziert), dann steht die Maschine für die Herstellung bereit (wir wissen allerdings noch nicht, ob das Produkt einwandfrei ist und wir wissen ebenso wenig etwas über die Produktionsgeschwindigkeit; wir wissen nur, dass sie läuft). Das Verhältnis von realer Herstellungszeit der Maschine zur theoretisch denkbaren Laufzeit der Maschine wird als Verfügbarkeitsgrad bezeichnet.
2. Mit welcher Geschwindigkeit läuft die Maschine?
Sofern die Maschine so generiert, dass sie zehn Stück pro Minute produzieren kann, dann werden sie vermuten, dass nach 360 Minuten 3600 Stück hergestellt werden. Dann beträgt die Maschinenleistung 100%. Ob dies der Realität entspricht, findet der Leistungsgrad hraus: er stellt die mögliche Ausbringung, also die Ausbringung, die die Maschine in der Theorie hätte erbringen können, sofern die Maschine während der realen Laufzeit mit Höchstgeschwindigkeit gelaufen wäre, der realen Ausbringung gegenüber.
3. Wieviele Produkte entsprechen der Spezifikation?
Nachdem Zeit- und Gewschwindigkeitsverluste gemessen wurden, rücken die Qualitätsverluste in den Mittelpunkt. Die Relation zwischen der Menge fehlerfrei produzierter Einheiten und der gesamten Menge produzierter Einheiten bestimmt den Qualitätsgrad.
Die Gesamtanlageneffektivität wird schließlich ganz einfach berechnet, indem das Produkt aus Verfügbarkeitsgrad, Leistungsgrad und Qualitätsgrad errechnet wird.
- OEE = Verfügbarkeit X Leistung X Qualität
Faktoren der Gesamtanlageneffektivität
Anlagenverfügbarkeit
- Formel: (verfügbare Zeit – Ausfallzeit) / verfügbare Zeit
Die Anlagenverfügbarkeit ist die Relation der Stillstandszeit zur theoretisch möglichen Herrstellungszeit. Die Stillstandszeit resultiert aus Zeitspannen für:
Rüsten
Der Anlagenproduzent demonstriert mit kompetentem Personal, dass die im Lastenheft relevanten Rüstzeiten unter Verwendung der im Pflichtenheft dargestellten Leitplanken (wie Hilfsvorrichtungen, Formatteile usw.) verwirklicht werden können.
Reinigung und Instandhaltung
Reinigung ist erforderlich, um den Herstellungszustand aufrechtzuerhalten und hygienische Anforderungen einzuhalten. Der Anlagenhersteller gewährleistet mit eigenem Personal oder unter dessen Anleitung die festgesetzten Reinigungs- und Instandhaltungstätigkeiten in der bestimmten Zeitspanne. Übereinkommen zu Reinigungszyklen und Reinigungsaufwand sollten vorab geregelt werden.
Störungen technischer Art
Unter Störungen werden Vorkommnisse verstanden, die streng ursächlich lediglich vom Abnahmegegenstand erzeugt werden und vertraglich einer Sonderregelung bedürfen. Dazu gehören Sachverhalte im vorgelagerten Prozess, beispielsweise kurzzeitige Schwankungen der Netzspannung.
Leistungsgrad
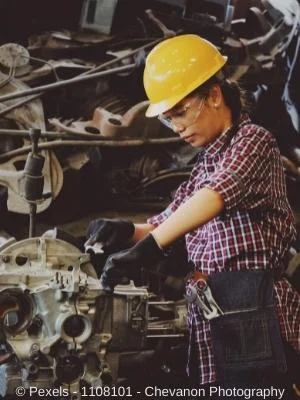
- Formel: Istmenge / (Nennleistung x Istzeit)
Der Leistungsgrad umfasst die real erreichte Leistung bezogen auf den festgelegten Leistungsumfang gemäß Lastenheft für die jeweilige WAre. Grundlage ist die Nettobetriebszeit (= theoretisch denkbare Herstellungszeit abzüglich Stillstandszeit). Der Leistungsgrad wird durch reduziertes Arbeitstempo vermindert, erzeugt durch Personal, Organisation, Qualität der Rohstoffe, Produkte sowie Packmaterialien oder Umgebungseinflüsse. Aus Sichtweise der Vertragsbeteiligten sollten während der Abnahme die vereinbarten Bandbreiten der Rohstoff- und Produktqualität für den Produktionsprozess berücksichtigt werden. Verantwortung für Personal, Organisation und stabile Umgebungsverhältnisse obliegen allein dem Anlagenbetreiber.
Qualitätsgrad
- Formel: (Istmenge – Ausschussmenge) / Istmenge
Der Qualitätsgrad ist die Relation von Gutmenge zur real eingesetzten Rohstoffmenge. Der Qualitätsgrad wird vermindert durch An-, Abfahr- und Spülverluste, Ausschuss, prozessbedingte Verluste (beispielsweise durch Ausdampfen). Durch Vorabfestlegung der Qualitätsmerkmale für Gutware, hinsichtlich der Zusammensetzung des Produktportfolios, können spätere Differenzen verhindert werden.
Beeinflussbarkeit der Gesamtanlageneffektivität
Die theoretisch größte Gesamtanlageneffektivität wird erreicht,
– wenn 100 Prozent der Betriebszeit (siehe Anlagenverfügbarkeit) hergestellt wird,
– wenn 100 Prozent der geplanten Geschwindigkeit (siehe Anlagennutzungsgrad) gefahren wird,
– wenn 100 Prozent der Produkte in der definierten Qualität (siehe Qualitätsgrad) hergestellt wird.
Differenzen von den 100 Prozent gelten als Verluste. Durch rechtzeitige genaue Untersuchung der Verlustfaktoren können Hinweise zur Optimierung der Maschinen und Anlagen gefunden und in die Herstellung mit berücksichtigt werden. Diese Untersuchung ist stets produkt- und projektspezifisch umzusetzen. Beispielsweise spielen Rüstzeitverluste bei Anlagen, die Monoartikel fertigen, nur eine untergeordnete Rolle. Bei Produktionslinien, die eine große Produktionsrange herstellen, können die Rüstzeitverluste dagegen in einer Größenordnung von 10 bis 40 Prozent liegen. Ebenso ist die teilweise sehr unterschiedliche Qualifikation und Verfügbarkeit von Bedienpersonal am jeweiligen Produktionsstandort Auswirkungen auf die Gesamtanlageneffektivität.
Der Personalaufwand wird bei der Gesamtanlageneffektivität nicht systematisch berücksichtigt und ausgewertet. Aus diesem Grund ist der quantitative und qualitative Personaleinsatz im Lastenheft explizit zu regeln – fallweise für den Produktionsvorgang, das Rüsten und Reinigen einer Anlage sowie für die geplante Instandhaltung.
Beeinflussbarkeit der Gesamtanlageneffektivität durch Anlagenlieferant und -betreiber
In die Gesamtanlageneffrektivität fließen sowohl Faktoren ein, die vom Maschinenlieferanten zu vertreten sind, als auch Faktoren, für die der Anlagenbetreiber verantwortlich ist. Beispielsweise hat der Lieferant von Maschinen, in Absprache mit dem Betreiber der Anlagen, eine Mitverantwortung bei der anlagenspezifischen Qualifizierung des Herstellungspersonals. Der Betreiber der Anlagen beeinflusst durch das zur Verfügung gestellte quantitative und qualitative Personal, ob eine höhere Gesamtanlageneffektivität realisiert wird oder OEE-Verluste in Kauf genommen werden.
Über die Selektion der technischen Lösungen werden die technisch begründeten Rüstzeiten, die Anlagenverfügbarkeit sowie die Lebensdauer der Teile wesentlich gesteuert. Im Zusammenwirken aller am Prozess der Beschaffung und Inbetriebnahme beteiligten Personen können optimale Ergebnisse erzielt werden: Ein integratives Projektmanagement sowie ein festrgelegtes Pflichten- und Lastenheft sind hierfür essenziell.
Projektmanagement
Grundbedingung für eine erfolgreiche Zusammenarbeit zwischen Betreibern der Anlagen und Loieferanten der Maschinen ist die Schaffung von Rahmenbedingungen, die eine vertrauensvolle, kooperative Zusammenarbeit gewährleisten.
Eine sinnvolle Projektorganisation ist möglichst zeitig zu schaffen und es sind Meilensteine zur Fortschrittskontrolle festzulegen. Alle, die einen gewünschten Beitrag zur Zielerreichung leisten können, müssen mitwirken. Auf Betreiberseite sind dazu beispielsweise Entwicklung, Technik. Produktion, Arbeitssicherheit, Instandhaltung, Reinigungsmannschaft, Einkauf und Qualitätsmanagement einzubeziehen. Seitens des Maschinenlieferanten müssen ebenfalls die jeweiligen fachlichen Kompetenzen bereitgestellt und gegebenenfalls Unterlieferanten und Dienstleister berücksichtigt werden.
Acht Schritte zur Einführung der Gesamtanlageneffektivität
Eine effektive OEE-Einführung verläuft in acht einfachen Schritten:
- Auswahl einer (Pilot-)Maschine
- Festlegung der OEE-Definitionen
- Entwurf von Erfassungsformular und -methode
- Training des Teams
- Erfassung der OEE-Daten
- Verarbeitung der OEE-Daten
- Feedback an das Produktionsteam
- Information des Managements
Fazit
An zahlreichen Maschinen und Anlagen zeigt sich, – nicht selten zum Unglauben der Mitarbeiter, aber vor allem des Managements – dass die Wirksamkeit der Anlage zwischen 30 und 40 % beträgt. Das heißt, dass es denkbar sein müsste, die gleiche Maschine oder Anlage mit verdoppelter Ausbringung laufen zu lassen (Steigerung der OEE von 30 auf 60 % oder von 40 auf 80 %) und damit noch immer freie Zeitfenster für Wartung, Rüsten usw. vorhanden sind. Erst wenn transparent geworden ist, wo diese „verborgene Maschine“ zu finden ist, wird man beginnen, sie zu sehen. Die Gesamtanlageneffektivität offenbart die „Verlustbrille“ und der TPM-Werkzeugkoffer die Verfahren zur Ausschließung dieser Verluste.